Lean and Safety
"...era già successo una volta ma si era fatto solo un graffio...”
Quante volte abbiamo sentito pronunciare questa frase, o una simile, in circostanze poco piacevoli?
Non tutti sanno che c’è una teoria che dimostra la stretta relazione tra un NEAR MISS (il graffio di cui parlavamo prima), un incidente di lieve entità e l’incidente fatale.
Questa teoria è spiegata dalla “Piramide di Heinrich”.
Si chiama piramide perchè ogni 300 “near miss” ci sono 29 “incidenti di lieve entità” e 1 “incidente fatale”, infatti è dimostrato che prima di un incidente fatale si sono verificati 300 NEAR MISS, che sono stati trascurati per mancanza di attenzione, e altri 29 incidenti di minore entità che hanno richiesto l’intervento dei sanitari.
Dare importanza al NEAR MISS consente di salvare tante vite ed evitare tanti incideni, ma va fatto nel modo giusto. Come?
Coinvolgendo direttamente il personale dell’attività considerata “a rischio” e dedicando tempo e risorse allo sviluppo della soluzione invece di spendere tanti soldi in un’attrezzatura, per esempio, che più o meno ci soddisfa dal punto di vista funzionale.
Il LEAN è un valido strumento per garantire la sicurezza senza sprechi, ma vediamo come:
GENBA WALK
È un mix di termini giapponesi e inglesi, GENBA indica “posto effettivo” mentre WALK significa “camminare”.
Camminare/osservare direttamente le attività sul posto reale in cui avvengono e segnalare quelle pericolose è alla base della cultura sulla Sicurezza e della filosofia Lean.
5 WHYS
In caso sia stato segnalato il NEAR MISS, la commissione/il gruppo di lavoro non deve fermarsi all’apparenza ma, facendo almeno 5 domande (5 whys) deve entrare nel dettaglio della dinamica per capirla fino in fondo.
7 WAYS
Una volta capita la dinamica, si cerca di impedire che questo possa riaccadere modificando un processo o progettando un’apparecchiatura che possa prevenire l’insorgere della medesima situazione di pericolo, senza impattare sulla libertà di movimento dell’individuo.
Ogni partecipante all’attività deve presentare 7 modi diversi (7 ways) di risolvere il problema, facendo dei disegni schematici.
Non verrà MAI implementata una soluzione così come proposta, la soluzione finale sarà frutto di una combinazione delle 3 soluzioni migliori.
In certi casi, si crede che la velocità di esecuzione sia la cosa più importante, ma quanto invece lo sia l’identificazione corretta dell’azione preventiva, non è chiaro a nessuno. Sviluppare una soluzione che sia d’intralcio all’operatore, indurrà lo stesso a non usarlo.
È per questo bisogna sempre coinvolgere chi è addetto alla mansione a rischio per renderlo partecipe nello sviluppo della soluzione, così che si senta a proprio agio nell’utilizzarla.
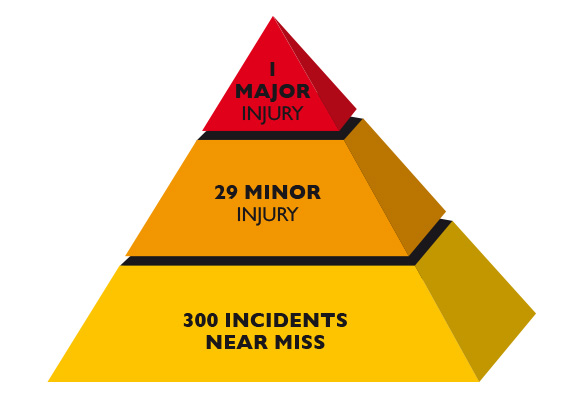